Three phase motors are reversible electric motors that can convert the rotational mechanical energy of their rotor into the alternating current (AC) power required for a specific load. This is accomplished by means of a revolving magnetic field generated by the rotor windings, which in turn induce a current across the rotor conductors. The induced current causes the rotor conductors to experience mechanical forces and this produces torque, which moves the rotor in the direction of the rotating magnetic field.
Three-phase motors are generally used for resistance heating loads, air conditioning, lighting and some other industrial applications requiring high efficiency and long life. In these cases, a three-phase supply is connected to the motor for efficient distribution of energy and to ensure stable power output at all times.
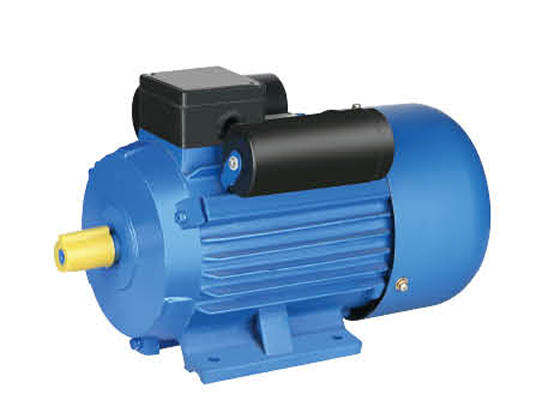
Control Systems
Large three-phase motors require a separate control circuit to turn on and off. This may be as simple as a single on/off drum-type switch or as elaborate as a digital variable frequency drive (VFD) unit.
Regardless of the power source and control system, the three-phase motor must be protected from excessive voltages that can damage the motor core and lead to excessive heat buildup. Some of the most common protection schemes include a soft starter and an in-built overload sensor that automatically shuts down the motor if a fault is detected.
Three-phase motors can operate on 230 and 460 volt AC systems, although 115 volt units can also be used. In these cases, the motor's nameplate is adjusted accordingly to compensate for the difference in rated volts per hertz between the two voltages.